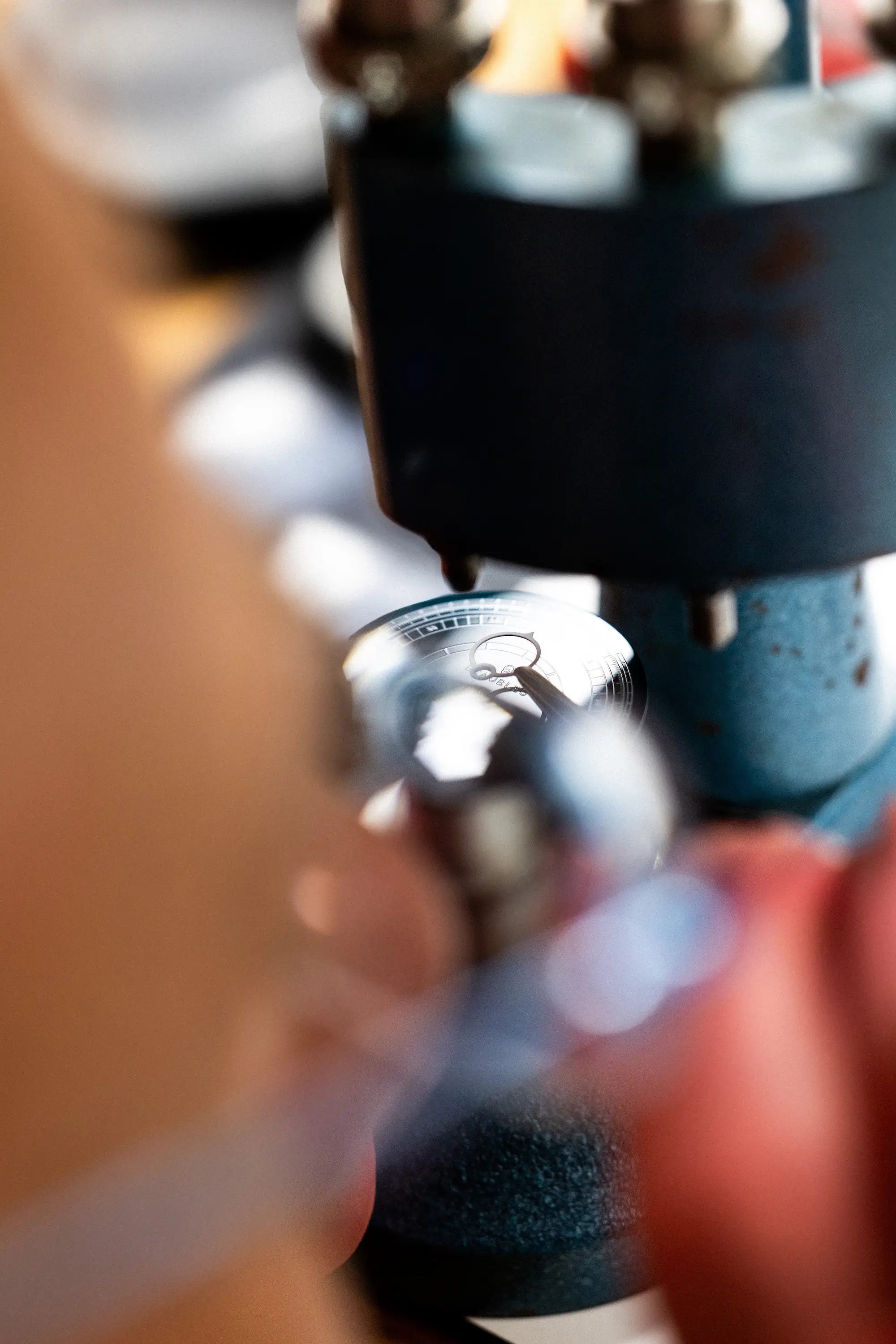
Seconde Française - Assembly
Behind the scenes of Beaubleu Workshops is revealed through the Production journey. A series of articles created to explain the stages of manufacturing Beaubleu watches and the challenges they raise.
When it comes to assembly (penultimate stage before control and shipping), the watchmakers at the Beaubleu workshop work meticulously to bring the hands, dials, cases and movements into harmony. Their role is to perfectly harmonize this whole to bring Seconde Française to life.
The movement
At the heart of the watch, the movement is like a symphony composed of nearly a hundred parts. Once assembled, they perform a dance of millimeter precision. Each mechanism is tested and adjusted with a margin of -7/+7 seconds.
Because we like to know what is happening around our wrists, the open case back, which is found on all Beaubleu models, will reveal the perfect symmetry and depth of the France Ebauches FE movement, made in France. The oscillating weight, designed in the image of the Maison's logo, hovers over a balance supported by two bridges, visible from all angles.
The next step: installing the dial.
Installing the dial
Once the movement is prepared, the watchmakers at the Beaubleu workshop position the two feet located on the back of the dial, on the plate. The latter thus supports all the components of the automatic movement.
The winding stem is then placed at 3 o'clock, and carefully screwed onto the side of the plate.
Laying the hands
After this, the hour hand is precisely aligned opposite the 12. Rotations are performed to ensure that it turns freely. The same precise dance is repeated with the minute hand, a few millimeters from the hour hand (0.2 to be exact), without touching it.
Positioning these round hands without altering them is a real balancing act. Each step has its share of checks, such as the placement at 6 o'clock to ensure their perfect alignment.
Otherwise, it's a step backwards: the hands are removed using a dial cover and a hand chaser, essential to avoid scratches.
Once this waltz is over, our watchmakers turn to the seconds hand, which for this collection, brings a special touch of magic to the whole. The 0.17 mm disc fits onto the barrel of the movement.
The slightest mishandling could damage the whole thing, so watchmakers must be extremely delicate.
Assembly
Before and after each manipulation, comes a crucial step: cleaning. A simple dust could actually require the complete disassembly of the watch.
Next, the winding stem is removed, and the automatic movement is placed in the case. Special attention is paid to the orientation of the movement, with the space for the winding stem facing the 3 o'clock position. After a cleanliness check (another one, but all these precautions are worth it), the winding stem is put back in place to hold the movement in position.
The now clean automatic movement is installed in the case, not forgetting the casing ring holding the movement. The case is then closed with four screws.
Next, it's time to cut the winding stem to the correct length, followed by filing and delicately screwing in the crown. A final careful check for dust and fingerprints, thus punctuating this assembly step.