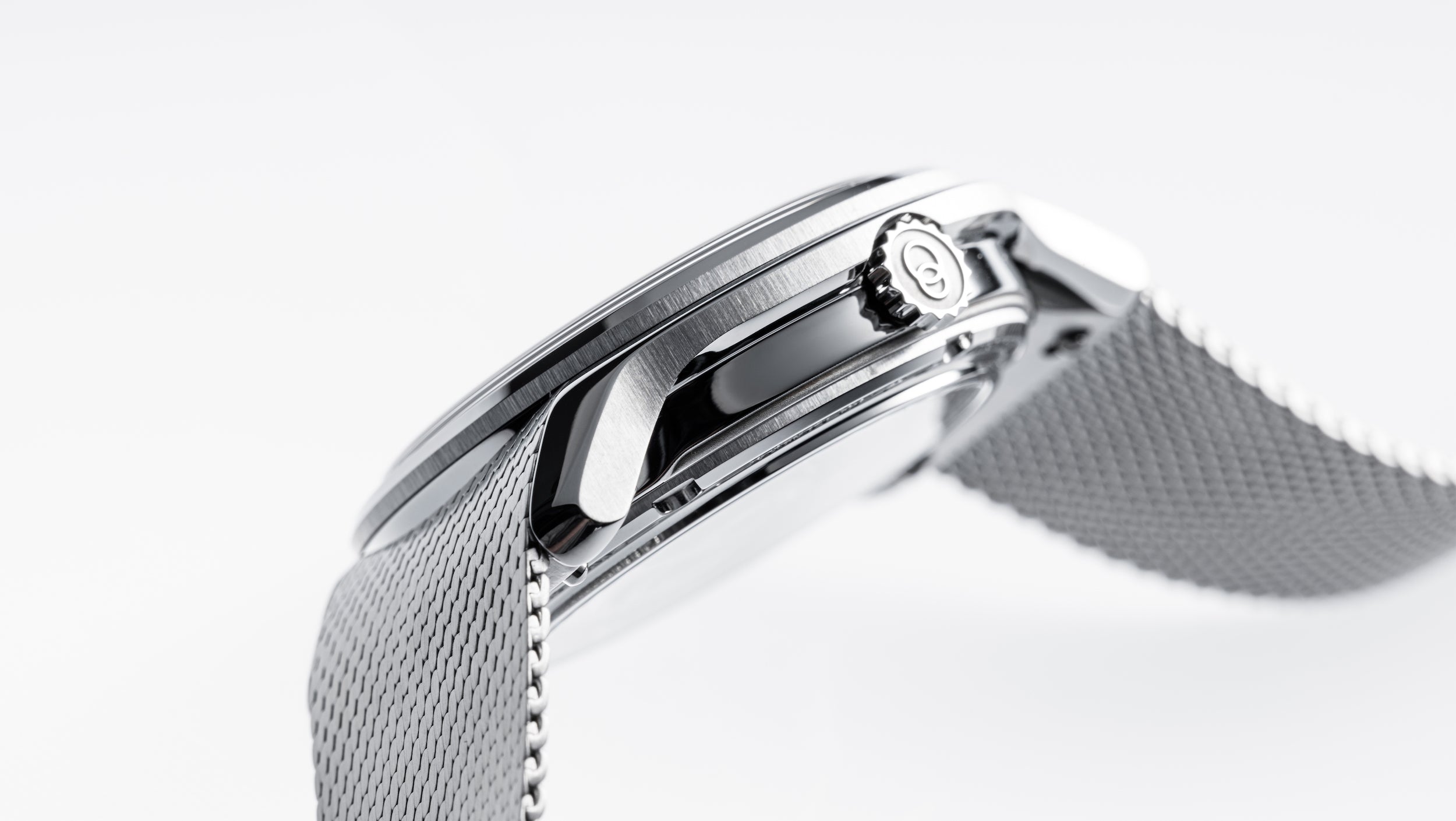
Seconde Française - The cases
Behind the scenes of Beaubleu Workshops is revealed through the Production journey. A series of articles created to explain the stages of manufacturing Beaubleu watches and the challenges they raise.
In this third episode, we focus on cases! From stamping to machining, as well as polishing, let's discover the transformation of a simple block of raw steel into a watch.
The cases
It all starts with blocks of steel, which are prepared to follow several stages, interspersed by measurements and finish types, until obtaining the final piece.
The first step is to shape the raw part by a series of compressions and flattening. For this, rolling mills are used (machines equipped with hardened steel cylinders).
This process has a crucial impact on the quality of the metal, making it both compact and robust. Each piece is subjected to rigorous dimensional control from the start, as the slightest variation can affect the final product.
Stamping
Stamping is similar to a form of die cutting, and involves shaping the case by using a punch to compress the material.
By repeating this operation several times, the metal gradually takes on the desired shape. After each stamping step, the part is annealed and then measured. It is at this stage that the first contours of the Seconde Française cases begin to take shape.
Machining
Once the stamping is complete, comes a step as complex as it is crucial: machining. This is where the magic happens, but be careful, a misstep here can be very costly!
The pieces are sculpted to their final shape, making sure they fit together perfectly. Holes are then drilled for the screws, and an overall check is carried out, from curves to corners.
This step brought its share of challenges (constraints, deformations, adjustments etc.) to then give way to the most exciting phase: the treatment of the surface aspects, giving the case this polished and brushed appearance.
Polishing
The pieces are meticulously polished using a lathe, where Beaubleu’s artisans focus on ensuring a flawless surface. Beyond avoiding scratches, special attention is paid to the interaction between light, the environment and the watch. It is comparable to examining a car body: reflections reveal whether the piece is perfectly smooth, curved or domed. It is truly an art mastered by experience, because a polishing error can require starting the piece from scratch.
Satin finish
This technique involves creating fine parallel scratches on the metal surface, resulting in a smooth and silky finish, with subtle shades of color that enhance the design of the watch. During this step, the polished parts are carefully protected with specific adhesive tapes, because the slightest overflow could require re-polishing, in the best case scenario.
Dual dome glass
For the Seconde Française collection, a dual-domed sapphire glass (exterior and interior) was used. The aim is to ensure that the curves of the glass modify the outline of the dial sufficiently to hide the edge of the seconds disc (a subtle optical effect), while ensuring perfect readability.
Control
Final step! A final check is carried out on the first steel cases to ensure perfect angles and sparkling surfaces. Some parts may require retouching in order to meet the strict Beaubleu quality standards.